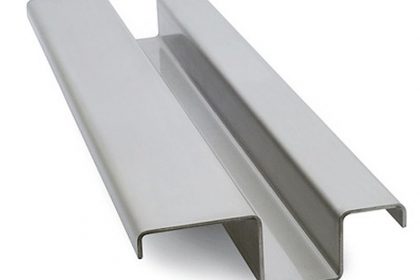
Why does a sheet metal CNC press brake bending machine need a mechanical compensation system?
Why does a sheet metal CNC press brake bending machine need a mechanical compensation system?
As we mentioned above, when the sheet metal CNC press brake bending machine is bending the workpiece, due to its own structural characteristics, under the action of the bending force, the upper and lower beams will produce deflection and deformation, which will cause the bending angle of the workpiece to be at the full length. The deviation in the direction is too large. The compensation system can effectively compensate the deflection and deformation of the sheet metal CNC bending machine. Using the compensation system on the upper beam or the lower beam can ensure the consistency of the bending angle over the full length.
According to its structure, the compensation system is divided into:
Hydraulic compensation system
Mechanical compensation system
- Hydraulic compensation system
The principle of the hydraulic compensation system is to embed several hydraulic cylinders in the lower beam of the sheet metal CNC bending machine. Each hydraulic cylinder can be controlled individually, so that the lower beam can form a certain bulge, as shown in Figure 1. . In theory, the more hydraulic cylinders used, the more compensation points, and the higher the compensation accuracy.
Hydraulic compensation is a built-in discrete compensation. In order to achieve high-resolution compensation, and then achieve higher bending accuracy, higher requirements are put forward on the number of hydraulic cylinders and their hydraulic control system, which leads to sheet metal The overall structure of the CNC press brake bending machine is more complicated and the cost is higher. The hydraulic compensation system cannot be applied to the customer’s existing sheet metal CNC press brake bending machine upgrade and transformation.
Figure 1 Schematic diagram of hydraulic compensation system
- Mechanical compensation system
The mechanical compensation system uses the filling method to compensate the lower beam/lower mold. The main principle is to generate different compensation curves through the mutual movement of a pair of deflection compensation wedges, as shown in Figure 2
Figure 2 Schematic diagram of mechanical compensation system
There are many types of mechanical compensation systems on the market. Take WILA’s mechanical compensation workbench as an example. It is an external, relatively continuous compensation, which is directly installed on the lower beam of the sheet metal CNC press brake bending machine and can be applied to new and old metals. The plate CNC press brake bending machine can continuously adjust different compensation curves for different applications, as shown in Figure 3.
Figure 3 Schematic diagram of mechanical compensation curve
Summarize
Both the hydraulic compensation system and the mechanical compensation system can effectively compensate for the deflection deformation of the sheet metal CNC bending machine. The difference between the two is in addition to the difference in the cost of the sheet metal CNC press brake bending machine caused by the different structure design, but also the compensation accuracy/resolution The rate of high or low. When dealing with high-precision bending applications, we recommend choosing a mechanical compensation system.