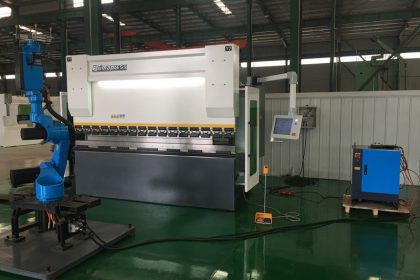
What is the prospect of robotic automatic cnc plate press brake bending machine?
In recent years, the application cases of industrial robots in China have increased rapidly, mainly focusing on welding, spraying, handling and other fields, but not many in bending. Workpiece bending is a widely used and dangerous work, so the market prospect of robot bending is very optimistic, and there are many successful experiences abroad. At present, 40%~50% of the cnc plate press brake bending machines in the sheet metal processing workshops in the European and American markets are equipped with robotic automatic bending systems, while the bending automation in China has just started. In the next 10 years, the demand for bending robots in China will rise linearly.
Robot automatic cnc plate press brake bending machine
The work of the bending unit is mainly divided into six processes: loading, picking, centering, turning, bending and stacking.
Loading: manually place the plates to be processed in a whole stack on the loading platform, and install the plate detection switch on the loading platform to prevent the robot from grabbing the tray after all the plates have been processed.
Reclaiming: When the robot runs to the position of the loading platform, it detects the height of the plate through the ultrasonic sensor installed on the grab. According to the detection data, it automatically runs to the appropriate position to grab the plate. After the plate is grabbed, it measures the thickness of the plate through the thickness measuring device to avoid grabbing more than one plate at a time, causing processing failures. After the thickness measurement is passed, it is ready for alignment.
Centering: the robot runs to the positioning table, places the sheet on the positioning table for precise positioning, and grabs the sheet again after positioning, ready for bending.
Turn over: judge whether it is necessary to use the turn over frame according to the process requirements. If necessary, move the robot to the position of the turn over frame, place the sheet on the turn over frame, and the robot will release the sheet and avoid collision. After the turn over is completed, grab the sheet.
Bending: the robot runs to the position of the cnc plate press brake bending machine, flattens the sheet metal onto the lower die of the cnc plate press brake bending machine, and accurately locates it through the rear finger sensor of the cnc plate press brake bending machine. After the positioning is completed, the robot sends the bending signal to the cnc plate press brake bending machine, and cooperates with the cnc plate press brake bending machine to complete the bending action, judge whether it needs to be bent again, and decide whether to perform continuous bending. Bending is a key link, and the technical difficulty of bending lies in the cooperation between the robot and the cnc plate press brake bending machine, that is, bending follows. When the robot clamps or supports the bending of the sheet metal, the sheet metal is deformed. The robot needs to follow the sheet metal to make an arc motion according to a specific trajectory algorithm, and always maintain a relatively fixed position with the sheet metal.
Stacking: When the robot moves to the position of the blanking table, due to the difference of workpiece forming, there are many kinds of stacking process actions, such as conventional matrix stacking, single and double layer cross stacking, positive and negative interlocking stacking, etc.
6-axis or 7-axis robot is equipped with 6+1 or (7+1, 8+1) axis CNC cnc plate press brake bending machine. Robotic full-automatic cnc plate press brake bending machine is used for sheet metal, which is equipped with centering table, turnover bracket and other accessories to meet the requirements of automatic bending. Advantages: labor saving, no potential safety hazard, suitable for long-term continuous operation, and good consistency of workpiece accuracy.
At present, whether it is a general standard six axis robot or a special bending robot for bending process optimization on robot arm span or body on the market, it needs to be supported by the bending following algorithm, and there are few cases that do not follow the bending. Without good following effect, the gripper or suction cup gripper will pull the workpiece due to poor following track, forming sheet wrinkles and affecting the forming quality. Establishing an accurate bending following motion model of the robot is helpful to establish a good tracking algorithm, so as to obtain excellent tracking effect.