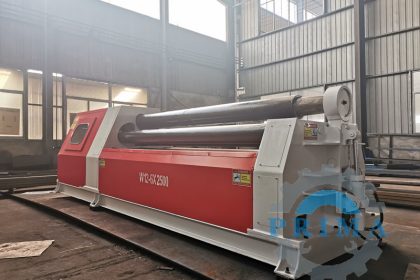
What are the differences between the two-roll rolling machine, three-roll rolling machine and four-roll rolling machine
In general, the working ability of the plate rolling machine refers to the thickness of the plate it can roll, that is, according to the specified yield limit, the plate in the cooling state is used to roll out the maximum thickness and width of the plate. the smallest diameter of talent. Under normal circumstances, the capacity of cold rolling is about half of that of hot rolling. But recently, the talent of the cold roll is constantly developing.
To sum up, according to the various types of coils, I have drawn up the following different plans, and analyzed and proved them separately.
Double Roll Rolling Machine Double Roll Rolling Machine Shows:
The two-roll plate rolling machine has only two rollers, the upper roller is a steel roller, and the lower roller is a roller with elasticity, and can also be used for straight motion. When the plate rolling machine starts to work, first the lower roller starts to make a rotating motion, which promotes the sheet material and the upper roller to press the sheet into the elastic layer of the lower roller under the action of the pressure of the movement, so that the lower roller is elastically deformed. However, the volume of the lower roller has not changed when the change occurs, so the pressure is transmitted to all sides, resulting in a strong and continuous back pressure, forcing the sheet to be closely attached to the rigid roller, and finally the sheet can be Roll out the barrel. The depth of the upper roller pressing the lower roller, that is, the deformation of the elastic layer, is the primary process parameter that determines the bending radius formed. Through many different tests, it is concluded that the larger the reduction, the smaller the bending radius of the sheet; but when the pressing amount reaches a certain value, the bending radius tends to be stable and has almost nothing to do with the reduction. This is an important feature of the twin-roll rolling machine process.
The double-roller plate bending machine has the advantages that other plate bending machines do not have: 1. The processed plate does not need to be pre-bent and can be directly processed, so the production speed is very fast; 2. The structure of the plate bending machine is simple and the price is low 3. About various Different types of materials can be processed. Disadvantages of the double-roller rolling machine: 1. Each product with a camber has a corresponding upper roller for processing, so it is not suitable for products that require different cambers in small batch production; 2. Generally, it can only be used for sheets below 10mm Thickness is processed, and the processing effect of too thick sheet is very poor.
Three-roll plate rolling machine (1) Symmetric three-roll plate rolling machine
The upper roller is symmetrically positioned at the center of the two lower rollers, the structure is simple and compact, easy to manufacture and repair, light in weight, low in investment, more accurate in forming, and the roller is less stressed, but it cannot bend the entire length of the sheet, and the two ends of the sheet are slightly The length less than half of the distance between the two lower rollers is straight, that is, the remaining straight side is large, and pre-bending equipment is required
Asymmetric three-roll plate rolling machine
The upper roller sits on top of the lower roller and is slightly offset, the structure is simple, and there are few straight edges left, but the sheet needs to be turned around and bent, which is inconvenient to operate, the roller is subjected to a large force, and the bending capacity is small. It is often used for rolling Thin and short light cylinder section, the working capacity is generally below 32×3000mm
Four Roll Rolling Machine
Four-roll plate rolling machine Four-roll plate rolling machine has four rollers, the upper roller is an automatic roller, the lower roller can move up and down, and the two side rollers can move up and down in an oblique direction! The four-roll CNC plate rolling machine is mainly designed for wind power towers. It can be used for the production and processing of various types of wind power towers. It is also used in shipbuilding, petrochemical, aviation, hydropower, decoration, boiler and motor manufacturing industries. It has been widely used in the field to roll sheet metal into various parts such as cylinders, cones and curved plates.
The four-roll CNC plate rolling machine produced by Primapress Machinery utilizes the spatial arrangement of its four rollers to minimize the appearance of remaining straight edges, reduce production costs, and improve production efficiency.
When the four-roll CNC plate rolling machine is rolling, the position of the upper roller is fixed, and the lower roller moves straight up to clamp the steel plate. The rollers on both sides move toward the upper rollers in a straight line or in an arc to adjust the radius of curvature of the roll. The four-roller and three-roller CNC rolling machines have different roller movements, but the working principles are the same. They all use the principle of three-point circle to roll with different radii. However, the pre-bending straight edge and the roundness of the rounding of the four-roll CNC plate bending machine are better than those of the three-roller; in the same time period, the processing efficiency of the four-roll CNC plate bending machine is twice as large as that of the three-roll CNC plate bending machine. .