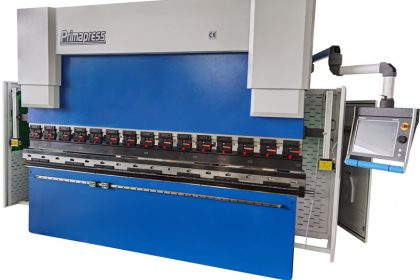
What are the development history of CNC bending machine and the advantages of hybrid CNC bending machine?
With the development of society, the increase of labor costs, and the continuous improvement of product requirements, many companies have continuously improved the performance and requirements of production equipment, and as an important production equipment in the forging and sheet metal industries-CNC bending machine It is also constantly updated and developed.
CNC bending machine
Let’s talk about the development history of CNC bending machine and the performance and advantages of the new CNC bending machine:
The CNC bending machine has changed from the previous simple CNC (mechanical synchronization)-electro-hydraulic synchronization CNC to servo control-hybrid servo drive control.
In 1970, CYBELEC launched the world’s first CNC bending system. In 1974, it introduced external memory instead of paper tape memory. In 1978, it developed the world’s first electro-hydraulic servo bending machine CNC system using microprocessor technology. In 1984, the first machine with graphics. Numerical control system for displaying and bending processes. In 1986, the first bending program with timely correction of angles. In 1987, the first numerical control system with three-dimensional graphics display. In 1990, real-time laser angle measuring device was used for bending technology. In 1998, real-time dynamic compensation was used. Technology, the first to use the CNC system of the Windows operating system. In 2002, launched the epoch-making digital sheet metal processing solution VPSS (Virtual Simulation System)
At present, the future trend of the sheet metal equipment industry is to develop in the direction of environmental protection, energy saving, high efficiency, and automation. The PM series hybrid CNC bending machine produced by Primapress came into being, which perfectly embodies the superior performance of energy-saving, high-efficiency, automation, unmanned and other aspects.
First, let’s take a look at the advantages of PM series hybrid CNC bending machine in terms of environmental protection and energy saving. Because PM uses the most advanced dual-servo pump control system drive in the world, we will call it (E-Z servo drive) for the time being. EZ servo pump replaces the traditional servo/proportional valve and control technology. This drive solution saves more space, hydraulic oil and energy consumption than ordinary hydraulic systems. The amount of hydraulic oil used is only 1/3 of that of ordinary hydraulic systems. –About 1/5.
The power consumption and energy efficiency of the servo-driven hybrid CNC bending machine are particularly eye-catching. Compared with the traditional bending system mode, the energy efficiency is very high, because the system only uses the energy required by the press brake in each stage. Most of the pressure drop from the bottleneck is reduced and offset, so the energy consumption can be increased by more than 75%. In the standby situation, the minimum is only about 5% of other systems. The position control accuracy of 5μm is the key to the system.
The performance of the servo-driven hybrid CNC bending machine in terms of high efficiency is the speed. Under the premise of ensuring the bending accuracy, its no-load and working speed can be increased by 15% compared with ordinary CNC bending machines– 25%, the return speed can reach more than 50%. This greatly improves productivity, and thanks to its own excellent hydraulic system, it can also keep the oil temperature within a stable range due to long-term fast reciprocating work. (The external environment temperature does not exceed 50 degrees Celsius when it is 38 degrees Celsius)
Pump-controlled servo-driven hybrid CNC bending machine can automatically select tools in terms of automatic functions, automatic program calculation, automatic robot bending, automatic laser detection, automatic feedback of detection results, identification, and then automatic compensation, including anti-collision Control, this is nothing, because it can realize unmanned operation in the true sense, and its perfect cooperation with robots can realize a truly unmanned chemical factory. The staff only need to operate the computer system in the office to complete the entire process of ordering-cutting-production-transportation-finished products, and can continue to work for a long time.
In summary, the PM series EZ pump-controlled servo-driven hybrid CNC bending machine produced by Primapress Machine Tool Co., Ltd. has reached the industry 4.0 standard in the field of artificial intelligence in the industrial manufacturing industry. It is a high-end CNC bending machine. It occupies an important position in the bending machine family and will also occupy a place in the field of China’s industrial manufacturing industry.