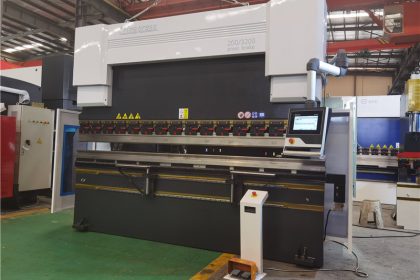
The main difference between hydraulic press brake and cnc electric hydraulic press brake machine
Both hydraulic press brakes and cnc electric hydraulic press brake machines belong to press brakes, just different categories.
The CNC bending machine is a CNC system added to the ordinary bending machine, and the bending style is realized through the programming of the CNC system, which can be said to be an upgraded version of the ordinary bending machine. Reduced labor and labor intensity. The mass production is realized and the production rate is improved. But one of the problems brought about is that the operation of the CNC bending machine has certain complexity and difficulty, and requires a certain knowledge base. There are some requirements for the operator’s education. Only in this way, the manufacturer can learn it during training.
The hydraulic bending machine is energized by the wire to the coil, and after the electricity is energized, the pressure plate is gravitational, so as to realize the clamping of the thin plate between the pressure plate and the base. Due to the use of electromagnetic force clamping, the pressing plate can be made into various workpiece requirements, and the workpiece with side walls can be processed.
The CNC bending machine has the function of multi-step programming, which can realize multi-automatic operation and complete one-time processing of multi-step parts.
The hydraulic bending machine includes a bracket, a worktable and a clamping plate. The worktable is placed on the bracket. The worktable is composed of a base and a pressure plate. The base is connected to the clamping plate by a hinge. The base is composed of a seat shell, a coil and a cover plate. The coil It is placed in the recess of the seat shell, and the top of the recess is covered with a cover plate. When in use, the coil is energized by the wire, and after the electricity is energized, the pressure plate is gravitationalized, so as to realize the clamping of the thin plate between the pressure plate and the base. Due to the use of electromagnetic force clamping, the pressing plate can be made into various workpiece requirements, and the workpiece with side walls can be processed.
CNC bending machine molds also have high requirements for strength. Castings are prone to bubbles in the production process, resulting in lower strength than forgings. Forgings are forged with air hammers, and the interior will be tighter and stronger. Large, so CNC bending machine molds generally choose forging instead of casting.
The hydraulic pad located between the punch and the slider is to compensate the deflection deformation of the slider and the worktable, so that the sheet metal contacts these three points along the full length of the die during the bending process. The length of the bending machine die is evenly distributed, so that the bending force of the punch is evenly distributed over the entire bending length. (The accuracy of the three-point bending angle can reach ±15″), the entire convex and concave die is composed of several 10, 20, 30, 50, 100 mm width block molds, and each punch is elastically supported, which can automatically adapt to the concave mold The highest bending straightness and a constant pressure distribution are ensured, which improves the accuracy of the bending angle and the straightness of the bending edge.
In fact, so many problems can be summed up in one sentence, that is: a CNC bending machine relies on a program to complete each process; a sheet metal bending machine is a single bending.
The CNC bending machine directly performs angle programming and has the function of angle compensation. The grating ruler real-time detection feedback correction, full closed-loop control, back gauge and slider dead gauge positioning accuracy is ±0.02mm.
The upper die of the CNC bending machine adopts a quick clamping device, and the lower die adopts a wedge deformation compensation mechanism. With multi-step programming function, it can realize multiple automatic operations and complete one-time processing of multi-step parts. According to user needs, the imported hydraulic system with stable performance and compact structure can be selected, and the back gauge can be driven by ball screw and synchronous belt.
The full name of the sheet metal bending machine is the hydraulic sheet metal bending machine, which adopts an all-steel welded structure and has sufficient strength and rigidity. Hydraulic upper transmission, the oil cylinders at both ends of the machine tool are placed on the slider to directly drive the sliding work. The slider synchronization mechanism adopts torsion shaft forced synchronization. The slider stroke is motorized and quickly adjusted, manually fine-tuned, and the counter is displayed.
In fact, we still want to talk about it and introduce the CNC bending machine in detail.
For the first processing, in addition to confirming the drawings, it is also necessary to consider the processing mold, the bending sequence of the workpiece, program input, etc. However, during actual processing, if the same workpiece needs to be processed again next time, it cannot be effectively called up. One-time processing and programming information can only be re-programmed to repeat the same work, also called “secondary repetitive operation”. In this case, it is a great waste of time and labor, repeated consumption, which leads to the processing efficiency of the bending machine. Decline. However, CNC bending machines can solve this problem, realize repeated batch bending, and improve processing efficiency. This is the difference between ordinary bending machines and CNC bending machines. This is also the intuitive technological change that CNC brings us. CNC era It’s here, and it’s also about the development path of Revolution 4.0.