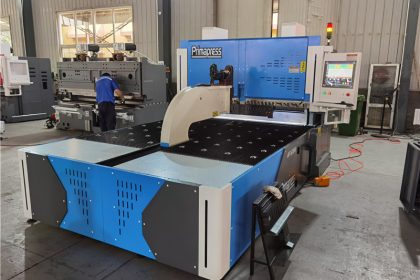
Primapress company develops and produces automatic bending center flexible bending center
Sheet metal bending equipment
Sheet metal bending equipment is divided into ordinary bending machines, CNC bending machines, edge bending machines, flexible bending centers and so on. Today, the editor takes the CNC bending machine folding machine as an example, and introduces the following in detail.
The CNC bending machine is to use the equipped mold (general or special mold) to bend the metal sheet in the cold state into workpieces with various geometric cross-sectional shapes. It is a sheet forming machine designed for cold-rolled sheet metal processing, and is widely used in sheet metal bending processing in automobile, aircraft manufacturing, light industry, shipbuilding, container, elevator, railway vehicles and other industries.
Bending dies are divided into standard dies and special dies according to the bending process. In the case of standard bending (right-angle and non-right-angle bending), standard molds are generally used for bending, and special molds are used for bending some special structural parts (such as step bending, dead edge, etc.). In addition, when bending sheets of different thicknesses, the selection of the “V”-shaped groove size of the opening size of the bending die is different. – Generally, the opening size of the “V”-shaped groove is 6-10 times the thickness of the plate (0.5~2.6mm is 6t, 3~8mm is 8t, 9~10mm is 10t, and 12mm and above is 12t). When the sheet is thinner, the orientation is chosen to be in a decimal number, and when the sheet is thicker, it is oriented in a large number. For example, 12mmV groove can be selected when bending 2mm board. The standard bending angle is generally not less than 90 degrees, and the sharp angle of the upper die and the lower die of the standard bending machine die is usually 88 degrees. In the case of non-standard bending, different upper die shapes can be selected, and different angles and shapes of the sheet can be bent. For sheet metal parts with special shapes, special bending dies can be selected for forming and bending.
CNC bending machine: The upper and lower dies are respectively fixed on the upper and lower worktables of the bending machine, and the relative movement of the hydraulically driven worktable is combined with the shape of the upper and lower dies to realize the bending and forming of the sheet.
CNC hemming machine: The motor drives the upper slider to press the sheet, and the hemming beam rotates from bottom to top, thereby driving the sheet to be bent and formed.
Compared with the hydraulic bending machine, the most characteristic feature of the CNC bending machine is its CNC operating system, which is an upgrade of the ordinary bending machine, which reduces the labor force of the operator and enhances the processing efficiency. But at the same time, the operation requirements and skills of CNC bending machine are much higher than that of hydraulic bending machine, and it is relatively complicated. The CNC bending machine has the function of multi-step programming, which can realize multi-automatic operation and complete one-time processing of multi-step parts.
The hydraulic bending machine is energized by the wire to the coil, and after the electricity is energized, the pressure plate is gravitational, so as to realize the clamping of the thin plate between the pressure plate and the base. Due to the use of electromagnetic force clamping, the pressing plate can be made into various workpiece requirements, and the workpiece with side walls can be processed.
Primapress company develops and produces fully automatic bending centers
Primapress company develops and produces automatic bending center to realize automatic bending function of four sides of the plate, which has the following characteristics:
1 Faster speed: Increase your efficiency several times, greatly reduce labor costs, and truly save time, effort and worry.
- Simpler operation: The labor requirements are greatly reduced, and the research and development is carried out according to the habits of the Chinese people, which is easy to learn and use, and relieves the trouble of personnel flow.
3 More energy-saving design: The product has high working efficiency, which can greatly save labor costs.
Primapress company develops and produces related products of automatic bending center-servo flexible bending center · second generation upper arm type · AT-S2000 is a servo flexible bending center developed by the company’s technology research and development department after two years of technical research , The bending speed only needs 0.2 seconds per knife, the equipment can automatically fold up and down according to the bending process to realize the combined bending of arc, dead edge and various angles, and the comprehensive average efficiency can reach the same specification CNC bending The bending machine is more than 3 times, saving a lot of labor and mold costs for the enterprise. The size of the processing plate is 1400x1400mm and 2000mmx1500mm, and it controls X, Y, C, V1, V2, Z1, Z2, W1, W2, P, a total of 10 axes. This bending center is all servo-driven, which fully saves energy and reduces consumption for enterprises. cost.
The CNC bending machine bends thin plates and produces workpieces of various shapes, so how to operate the CNC bending machine correctly? The following are practical bending machine operation skills:
Turn on the power first, then turn on the switch and then start the oil pump. This sequence must not be confused. The operator starts to operate the CNC bending machine by listening to the sound of the oil pump turning.
Second, it is necessary to step on the foot switch to perform the bending process to avoid mistakes in the work of the operator
- Pay attention to the size of the bending notch, and it is most suitable to have a width of eight times the thickness of the plate.
- Appropriate tests should be carried out before operating the CNC bending machine. Carefully check whether there is a gap between the lower die and the bottom of the upper die, and the size of the gap needs to be well controlled.
Flanging machine and hemming machine are the most common names in the industry. Generally, we call it a servo flexible bending center or a panel bending center. It can produce many of the same geometries as a conventional press brake, with the added benefit of making certain parts easier to produce, all using standard tooling.
Anyone familiar with flanging machines knows that the speed of a servo-flex flanging center is unmatched when producing traditional box-shaped parts. These machines can produce boxes, lids and other similar shapes in a very fast and precise manner due to the way in which the center of the hem creates a bend. The hemming machine can bend the entire side of the box at once, and it can even handle return flanges on the box with ease.
Using the hemming center allows the raw material to be loaded directly into the table and processed by a single operator in minimal steps. The advantage of the hemming center is that it is easy to highlight on large panels, especially the clamping of sheets that can be set automatically.