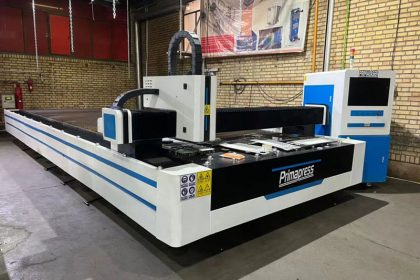
Power development trend and prospect of fiber laser cutting machine for sheet metal
Fiber Lasers Drive Industry Revolution
The great development of fiber lasers in the past decade is the most revolutionary technological breakthrough in the laser industry, especially in the Chinese market. From the earlier pulsed fiber laser marking that quickly swept the marking market, after 2014, fiber lasers were used in metal cutting to rapidly increase volume. The capabilities of fiber lasers shine in industrial processing applications, and they have now become the most important type of industrial lasers, accounting for more than 55% of the world, and they are widely used in various aspects. Laser processing technologies such as laser welding, laser cutting, laser marking and laser cleaning have jointly promoted the development of the entire laser industry market.
China is the world’s most important fiber laser market, with current market sales accounting for about 60% of the world’s. The installed capacity is also second to none in the world. The installed capacity of pulsed fiber lasers has already exceeded 200,000 units, and the installed capacity of continuous lasers is also nearly 30,000 units. Major foreign manufacturers such as IPG, nLight, and SPI regard China as the most important market, and in fact their sales in the Chinese market account for more than 40% of their company’s sales.
Fiber laser equipment power improvement competition and development path
It is understood that the trend of high-power development in laser processing is also very obvious, and the limit of cutting thickness is constantly being explored. The data shows that the average installed power of the overall market has increased year by year since fiber lasers became the mainstream of cutting applications.
In 2014, laser cutting applications became mainstream. The 500W power laser of the year quickly became the darling of the market. It then quickly evolved into kilowatts of power to 1500W.
Before 2016, the world’s major laser equipment manufacturers believed that 6KW could solve most of the cutting needs. However, in the second half of the year, Han’s Laser took the lead in launching an 8KW laser cutting machine, which opened the competition for laser equipment power improvement.
In 2017, the 10,000-watt laser cutting machine was born, and the Chinese metal sheet fiber laser cutting machine market began to move towards the 10,000-watt era, and even the subsequent 20,000-watt and 30,000-watt lasers came into being. High-power fiber lasers are like a race. It is difficult to say whether the demand for laser processing drives the power of the laser, or whether the increase in the power of the laser promotes the ultra-high-power laser equipment.
Market Choice and Rational Thinking
In this round of laser cutting equipment power competition, Chinese manufacturers are obviously leading the world, even earlier than foreign giants. Until a certain exhibition in Shanghai in 2019, the major cutting equipment companies were still scrambling to launch 20KW equipment, and even claimed to have 30KW equipment, which seemed to be a bit obsessed with power chasing.
There is no denying that domestic brands such as Raycus, Maxphotonics, JPT, Feibo, Guozhi and other companies have continuously launched fiber lasers above 10,000 watts, and foreign IPG, nLight and SPI are also advancing, contributing to the development of fiber lasers. It has made important contributions and opened up more application spaces and possibilities for laser processing. It is not denied that the increase in power will bring about higher processing efficiency. For the same thickness of metal plate, the most popular 12KW laser cutting machine with ultra-high power at present, its processing speed efficiency is almost twice that of 6KW. With the continuous improvement of the performance and efficiency of high-power fiber lasers, the efficiency of laser processing has been greatly improved, and generalized tools may be manufactured for large-scale production in the future.
However, we must see that most of the metal materials with a thickness of more than 40 mm appear in high-end equipment, large components, and special fields and special applications. Most common products in life and industrial manufacturing require laser processing within 20 mm, which is precisely the range of 2000 to 8000 watt lasers. On the one hand, we see that foreign companies such as TRUMPF, Amada, Mazak, etc. do not deliberately pursue rendering 10,000-watt cutting equipment, but focus on recommending appropriate power according to user processing conditions. On the other hand, we have also seen that users are gradually becoming rational, and market choices gradually show that the growth in shipments of cutting equipment above 10,000 watts has not reached expectations, but instead, the medium and high power 2KW to 8KW has increased rapidly.
Laser manufacturers are still working hard to increase the power of the light source, but having this power capability does not mean that the market can form batches. In addition, whether the power carrying of optical devices and supporting integrated products can be followed up is also a big problem. In addition, to increase the processing speed is not to blindly increase the power, but also to work hard on mechanical factors such as integrated machine tools, control systems, motion tables, and full-body design. Users are very aware of their product and processing needs, and they will eventually rationally choose a power segment that suits their application. What they value most is the stability of high-power machines and the ability to continue processing.
Today, the laser processing power has formed a pyramid-like layering. At the top of the pyramid, the ultra-high-power parts above 10KW account for a minority, and the power level will be higher and higher. The medium and high power part from 3KW to 10KW is currently the fastest growing field. Bottom applications belong to the cutting market below 2KW. Returning to practical applications, the batch of ultra-high power is not large. At the real application level, the consumption of 2000-8000 watts is returning rapidly.
This pyramid structure is not static. The author predicts that in the next five years or so, the domestic laser cutting market structure will change to “small at both ends and big in the middle”. Because small and medium-power CW lasers are very cheap at present, it is very easy for 3KW and 4KW equipment to cannibalize 1KW or 1.5KW, but it is not so easy to cannibalize 3KW, 4KW and 6KW above 12KW .
Advance the layout of the future medium and high power laser market
The laser industry is an industry with obvious globalization characteristics. The raging of the new crown pneumonia epidemic from 2020 to 2022 has caused many laser companies’ orders to suffer from Waterloo. An accompanying phenomenon is that the epidemic has hit users’ investment confidence, people’s investment tends to be conservative, and the average power of the factory laser equipment drops very quickly.
However, in May, the epidemic situation in my country has basically subsided, and various industries have recovered rapidly. In addition, the support of various national policies has increased, and the demand for laser manufacturing has rebounded rapidly. In mid to high power applications, 3000 to 8000 watts are still the most interesting. The main reason is that this power segment can meet most processing needs, has formed a mature and complete industrial chain in the market, and is cost-effective in general application scenarios. Therefore, it is foreseeable that in the next few years, the medium and high power market capacity will be the largest.