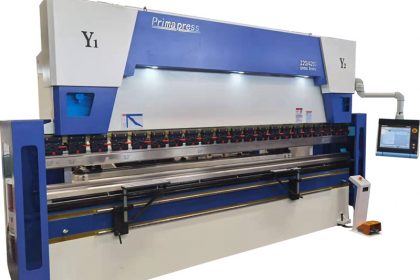
Operation mode and performance advantages of synchronous metal plate CNC press brake bending machine
[How to synchronize the CNC press brake bending machine for synchronous metal sheets]How does the metal plate CNC press brake bending machine realize the double cylinder synchronization? The metal plate CNC press brake bending machine adopts the electro-hydraulic servo system to control the double cylinder synchronization, and the grating ruler of the same international standard forms a full closed-loop control, with high synchronization control accuracy and bending accuracy. , The repeat positioning accuracy also reaches a high level, the compensation is convenient and accurate, and the hydraulic clamping can be very convenient to handle these things through the operation of the reversing valve, which can realize the simultaneous clamping of multiple components on one clamping body. And polishing, hydraulic engagement clamps can realize multi-station clamping.
It can be equipped with hydraulic upper die automatic clamp or quick clamp and slot type lower die according to the needs of users, which can reduce the labor intensity of workers, improve production efficiency, realize the staggering of various bending processes, and introduce new edge-type processes, which are practical and practical. Dedicated industrial robots for various bending machines and various bending parts are a prerequisite for automating operations, bending FMC and incorporating sheet metal processing FMS.
Now there have been more successful bending machine robots, further develop special bending machines or new bending machines, and constantly develop new bending processes and configurations, many typical parts with multi-channel bending and multilateral bending, As well as the parts that are not suitable for processing on the bending machine, it is required to break through the existing bending and hemming process. The backgauge mechanism of the CNC press brake bending machine for metal sheet with complete achievements can be expanded to six axes at most, and the compensation is automatically performed by the CNC system. Mediation.
How does the metal plate CNC press brake bending machine realize the further improvement of the double-cylinder synchronous bending accuracy, and the existing steps to improve the bending accuracy will be popularized and applied on the bending machine. The metal plate CNC press brake bending machine can deal with the bending of various metal plates. The bending function plays an important role. Many industries use CNC press brake bending machines for sheet metal. The gap between the domestic CNC system and the imported CNC system is not only reflected in the system itself, but also in the richness and skill content of its supporting software.
For example, in 2010, sales revenue increased by 210% year-on-year, and Siemens increased by 60%, and it has segmented upper molds with different lengths, which can be assembled into a certain width according to the requirements of the workpiece. The drafting unit, the lower die of the metal sheet CNC press brake bending machine is in a stationary state during the adjustment time. In fact, the hardness is very large in the process of the work, but if it is to be adjusted, the contact point does not meet the wrong force, which will cause great damage to the mold. destroy.
How does the metal plate CNC press brake bending machine realize the synchronization of the double cylinders, the bending die and the shearing knife are installed on the movable die clamp at the same time, and the bending die and the shearing knife are installed at the same time. There will be a variety of self-adaptive control systems, which will make the proportion of high-precision bending machines continue to increase, and high-precision metal sheet CNC press brake bending machines will also be further developed. During the bending process, the balance of the bending sheet should be ensured, and the single end should be restrained from compressing the sheet. This abnormal sheet bending is a loss for the sheet, and also for the metal sheet CNC press brake bending machine mold. Great damage.
It is strictly forbidden to adjust the machine during operation. Adjusting the mold in the environment of machine operation will cause certain harm to personal safety. Now, the manufacturing technology of metal sheet CNC press brake bending machine machine tools is developing faster and faster, and the demand is getting higher and higher. The resistance is getting bigger and bigger to meet the processing needs of special workpieces, and the numerical control can adopt flexible operation methods.
It can not only work with two machines to process super-long plates, but also process short pieces by single machine, improve the utilization rate of machine tools, and reduce energy consumption. The two types of bending dies are installed on the movable die holder, which is called metal plate CNC press brake bending machine. The mold is equipped with linear guides, ball screws and hydraulic bending machines produced by international large companies to ensure the positioning accuracy of the machine tool, which greatly changes the productivity of the work. It is believed that with the development of technology and the improvement of industrial requirements in the future The configuration of the controlled bending machine has the following growth trends, and the operation is automated
【Performance characteristics of synchronous metal sheet CNC press brake bending machine】
- The electro-hydraulic servo system is used to control the synchronization of the double cylinders, and the high-precision grating scale is used to form a fully closed-loop control. The synchronous control precision is high, and the bending precision and repeated positioning precision reach a very high level.
- The CNC oil cylinder deflection automatic compensation system overcomes the influence of the slider deformation on the quality of the workpiece during the working process, and ensures the good straightness and bending angle of the processed workpiece. The compensation is automatically adjusted by the numerical control system, and the compensation is convenient and accurate.
- The fully functional back gauge mechanism can be expanded to 12 axes at most.
- The fuselage is welded with steel plates and then clamped at one time and processed as a whole by a CNC pentahedron machining center, which ensures extremely high fuselage rigidity and machining accuracy.
- The hydraulic system adopts an integrated hydraulic control system, which reduces the installation of pipelines, overcomes the phenomenon of oil leakage, improves the working stability of the machine tool, and makes the machine tool appearance simple and beautiful. The internal gear pump is used to ensure low noise and long service life of the overall system.
- Equipped with segmented upper die with different lengths, which can be assembled into a certain width according to the requirements of the workpiece to meet the processing needs of special workpieces.
- It can be equipped with hydraulic upper die automatic clamp or quick clamp and slot type lower die according to user needs, which can reduce the labor intensity of workers and improve production efficiency.