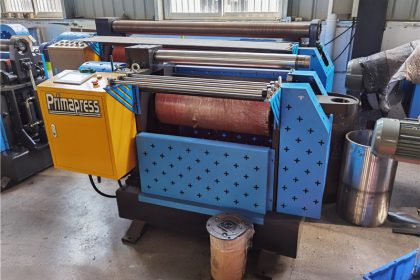
More knowledge about automatic CNC two-roll plate rolling machine
The specification of the automatic CNC two-roller plate rolling machine is flat and the plastic metal plate is determined between the three working rollers (two lower rollers and one upper roller) of the hydraulic automatic rounding machine, with the help of the lower pressure of the upper roller and the rotation of the lower roller. , so that the metal plate is continuously bent in multiple passes. And produce permanent plastic deformation, rolled into necessary cylinders, cones or a part of them. The disadvantage of the automatic CNC two-roll plate bending machine is that the end of the plate needs to be pre-bent with other equipment.
The automatic CNC two-roller plate rolling machine is suitable for large-scale CNC two-roller plate rolling machines with a thickness of more than 50mm. A row of solid idlers is added to the lower part of the two lower rollers. Usually, the operation efficiency and failure rate of mechanical equipment are similar to those of operators. The relationship between them is very close. As an operator of dangerous equipment, you should know more about the relevant knowledge in order to effectively avoid some misoperations or accidents caused by the operator. Let’s take a look at the safety requirements for the operation details of the CNC two-roll plate rolling machine.
First of all, the operator should tidy up the environment around the operation before operation, maintain a good operating environment, and at the same time, the operator must be neatly dressed to avoid pulling the corners of clothes into the roller during the operation. During the process, it must be noted that the operator can only stand on both sides of the workpiece, which is the most reasonable position. If you want to adjust and measure the roundness during the operation, you must stop the operation, and it is forbidden to operate during the operation. A certain margin should be left at the end of the processing part.
About the components of each device of the hydraulic automatic crimping machine
The hydraulic automatic crimping machine is composed of a frame, an automatic lifting mechanism and an automatic hemming mechanism. It is characterized by a threaded clutch welded on the frame. 120-degree distribution, the rotating rod has a roller at one end and a roller at the other end. The motor drives the main shaft to drive the automatic lifting mechanism and the automatic hemming mechanism through the worm gear and worm drive, and the entire hemming process is automatically completed. The utility model has the advantages of simple operation, flexible use, low cost and high efficiency.
The spindle is divided into five sections, three straight sections and two threaded sections. There are three rotating rods, distributed 120 degrees. The rotating rod has a roller at one end and a roller at the other end. The utility model has the advantages of simple operation, flexible use, low cost and high efficiency.
Working principle: Through the high-speed rotation of the workpiece, the upper and lower parts of the workpiece are extruded and deformed to form a curling effect. Each part of the automatic CNC two-roller plate rolling machine: 1. Mechanical part: frame, tail end, carriage. 2. Electrical part: hydraulic station, motor, cylinder or cylinder
Automatic hemming machine is a kind of good mechanical equipment, then we will play the role of automatic hemming machine in the work of industrial production. The above knowledge about automatic hemming machine hope that you will have a good understanding of automatic hemming machine. Deeper understanding.
What are the operating steps of the CNC two-roller plate rolling machine when rolling sheet metal
The overall arrangement of the CNC two-roller plate rolling machine equipment consists of three parts: bracket, worktable and splint. In use, the wire is energized with the coil. After the power is turned on, the pressure plate is attracted, and the clamping between the pressure plate and the base is completed. When you know how to use it, you will find that the CNC bending machine is very simple. Without further ado, let’s take a look at the situation of CNC two-roll plate bending machine manufacturers using CNC two-roll plate bending machines:
The first step is to turn on the power. Turn on the switch on the control panel and start the oil pump. Do not do anything when you hear the sound of the oil pump being replaced.
The second step, stroke conditioning, pay attention when using it. You have to pass the test to yield. There must be a gap of plate thickness at the bottom of the upper die, otherwise it will cause damage to the die. Stroke adjustment has electric speed regulation.
The third step, the selection of the bending notch, usually chooses the thickness of the plate to be 8 times the width of the notch. For example, when bending 4mm sheet material, a gap of about 32 should be selected.
The fourth step is to adjust the rear gauge to electric speed regulation and manual speed regulation.
Step 5. Step on the foot switch to start bending. The CNC bending machine is different from the CNC shearing machine. You can release the foot at any time. If you release the foot, it will stop, and then go down the steps continuously. CNC bending machine is directly bent, no need for splicing, no need for grooving, no need for welding rod, its folding corner surface is beautiful and does not leak, welding technology is operated in automatic machine tools, improving product quality, improving work efficiency, reducing labor costs, and greatly shortening the product production cycle.