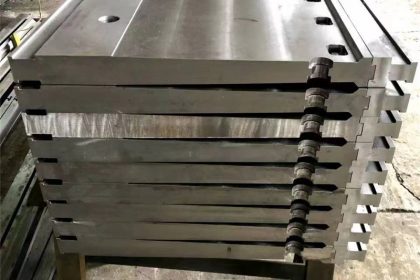
How to choose a sheet metal cnc press brake bending machine mold?
The bending mold is generally composed of an intermediate plate, upper mold, lower mold, guide rail, and lower mold seat. This type of mold has strong universality and most processing can be completed.
1、 Understand the variety and parameters of molds
When using a sheet metal cnc press brake bending machine in practice, it is necessary to have an understanding of the processing parameters of the sheet metal cnc press brake bending machine mold in order to select a matching mold for different sheets that need to be equipped with different sheet metal cnc press brake bending machine molds.
Upper mold part: straight sword knife, straight sword (large, small) curved knife, gooseneck (large, medium, small) curved knife, 30 degree sharp knife, flattening knife, simple mold, special mold, arc cutting tool, etc.
Lower mold part: Double V-groove V4-V7 V5-V9 V6-V10 V7-V11 V8-V12 V15-V18, etc.
Single V-slot V4 V5 V6 V7 V8 V10 V12, etc.
Mold base part: single slot mold base and double slot mold base. There are three types of double groove stations: low station (55cm), medium station (75cm), and high station (135cm).
2、 Selection of mold material
Due to their different structures, different materials use different cutting tools, resulting in different acid and alkali resistance, tensile strength, material hardness, tensile coefficient, plasticity, etc. When selecting a mold, reasonable selection can be made based on the pressure, structure, material, workpiece development size, process requirements, surface treatment, etc. of the machine tool.
In general, for iron plates, the slot width of the lower mold can be selected to be 5-6 times the material thickness, not less than 4 times, and not more than 8 times. The notch of the stainless steel lower mold should be 6-8 times the material thickness and not less than 5 times. The groove of the lower mold for aluminum and copper can be selected to be 8-10 times the thickness of the material (to avoid surface cracks during bending)
3、 The issue of workpiece and avoidance
The selection of the upper mold is reasonable based on the structure of the workpiece, such as avoiding position, avoiding nails, avoiding nuts, etc. When the workpiece needs to avoid position left and right, a bending knife can be selected, or many machining parts require a single V or double V groove lower mold. When bending the workpiece, the V groove should be selected based on the thickness and hardness of the plate. Generally, when T ≤ 4mm, the V groove is ≤ 24mm, while when T ≥ 4mm, the V groove is greater than or equal to 32mm. At the same time, it should be noted that if the workpiece needs to be bent at 90 degrees, In order to avoid mold damage or scrapping of machined parts, the V-groove should not be less than 4t, and various abnormal conditions that may occur during the molding process should be considered during operation.
When the ratio of V-groove to material thickness is 6 times, the unfolded size of the workpiece should be increased or decreased by 0.10mm for every increase or decrease of one unit (1mm). When it reaches its limit, there is no significant change.
The selection of special molds is based on the shape, performance, size, appearance, and safety height of the machine, as well as the pressure of the machine, etc. of its structure. The adjustment of segment difference mold is to adjust the amount of filling material in the middle of the mold according to the size requirements of the workpiece segment difference to control the size of the workpiece.