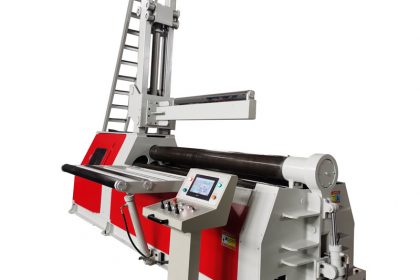
Function introduction and operation process of sheet metal plate rolling machine
Function introduction of sheet metal plate rolling machine
- The sheet metal plate rolling machineadopts the domestic transverse dynamic system design, not under the platform. The torque of the electric motor is fully utilized.
- The rear oil station is welded on the frame to improve the bearing capacity and firmness of the whole metal sheet rolling machine. The cooling water circulation pump is added to ensure the hydraulic stability of the hydraulic coiler in long-term work or in high temperature climates.
Function introduction of rolling mill
- The high-pressure hydraulic cylinder can achieve synchronous vertical lifting under the limitation of the photoelectric switch, and there will be no shaft bending accident due to misoperation.
- Operate the switches and buttons on the electronic control box in the “manual” state, adjust the stroke, limit and connecting rod of the hydraulic cylinder through point movement; after the test, when entering mass production, the switch is switched to “automatic”. Only the foot switch can realize the “dumb” key operation to complete the AUT process.
Function introduction of sheet metal plate rolling machine
- Application of twin-roll forming technology: After cutting the upper roll and chrome plating, the surface has good flatness and wear resistance; the seamless steel pipe is used as the inner core of the lower rubber wheel, and the polyurethane is wrapped on the outside. When the sheet is rolled up automatically, it does not scratch the inside and outside of the metal sheet, and it is not necessary to pre-bend both ends of the sheet. Only the foot switch can realize the “dumb” key operation to complete the AUT process.
- The sheet is rolled through two rolls on each part, so no pre-bending is required and there are no “straight edges” at both ends. Therefore, the roll has good roundness characteristics compared to the three-roll roll.
Scope of application:
Suitable for rolling the corresponding sheet metal into cylinders of larger diameters and lengths.
What are the security operating procedures of the sheet metal plate rolling machine
- Bending operators must be familiar with all switch and button functions of the equipment. Before beginning to ensure proper operation, check the adjusting screw and control switch
- Operators must fasten their clothes and cuffs, and are not allowed to wear aprons and noodles. Women with long hair should curl their hair and wear a hat to prevent security incidents.
- Before starting the device, add proper grease to the drive and sliding surfaces. The next step can only be performed when the equipment is functioning properly, flexibly and reliably.
- Obstacles must be removed before starting the machine. No one is allowed to stand in front of the machine.
- Adjust the position of the roller according to the diameter of the rolling ring. Use scrap for debugging before operation, do not directly bring workpieces for debugging.
6 When operating, the distance between hands and other parts of the body should not exceed 20 cm from the roller. It is strictly forbidden for non-operators to stay in front of the equipment.
- If an abnormality is found during operation, please stop the inspection immediately and continue to operate until the fault is eliminated.
- The processed workpiece should not be placed directly on the ground, but should be placed on the floor or on the material cart. They should be stacked neatly and not so high that they obstruct access.
- Clean up oil and debris on machine tools and molds, maintain and maintain equipment, and clean up the surrounding environment after get off work.
The metal plate bending machine must be well grounded, and the wire must be no less than 4 mm2 copper wire. Do not exceed the specified range to access the supply voltage. Do not use a megawattmeter to plug in or test control circuits. Otherwise, the device may be damaged
When inserting and removing plug-ins, do not unplug wires or cables to prevent the weldment from being pulled out.
Proximity switches, encoders, etc. are not affected by hard objects.
The sheet metal bending machine display cannot collide with sharp objects.
The electrical box must be placed in a well-ventilated area and must not be exposed to dust or corrosive gases.
Installation or reconnection of PC inputs and outputs is not permitted without permission.
When replacing the power supply of the machine, the direction of the motor must be reconfirmed.
Machine tools should be kept clean, paying particular attention to chutes such as clamping blocks and slides.
Periodically add lubricant to chains and other sliding parts.
Power must be disconnected during cleaning and maintenance.
Preparation before starting: Check whether the oil level of the fuel tank reaches the oil level line, add oil to the lubrication point, confirm the motor steering, whether the oil pump has abnormal noise, whether the hydraulic system leaks after starting (the angle encoder does not allow refueling); Pressure adjustment: use electromagnetic pressure release The valve regulates the pressure to ensure that the system pressure reaches the desired working pressure, usually no higher than 12.5 MPa.
Die adjustment: Die installation requires the die and clamping block to be aligned, and the clamping block can be adjusted with bolts; booster module and die centering, booster module is adjustable; core and die centering, core frame bolts are loosened and the center is adjusted after the bolts are tightened .