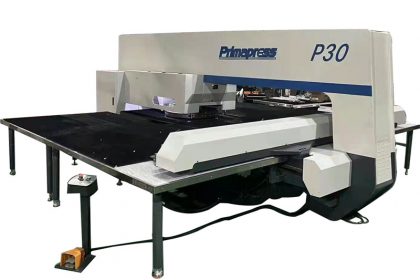
Forming and burr problems of metal sheet CNC turret punch punching machine forming die
- The forming direction of the forming mold should be selected to form upward as far as possible, and the collision between the formed shape and the steel ball on the workbench should be avoided as far as possible to avoid product deformation.
- When using the forming die, the CNC punchmachineis strictly prohibited from punching without a plate, and the die cannot be punched empty. At the same time, the tightness of the locking screw should be checked frequently, otherwise it will easily lead to damage to the CNC punch and the forming die.
- The closing height and stamping stroke of each CNC punching machine are different, so each set of forming molds must be adjusted to the shortest time when using it, and it should not be used directly on another punching machine. It needs to be fine-tuned before use. , to avoid damage to machine tools and molds.
- The lower die of the upward molding die is usually higher than the standard lower die, so try not to use the punching die station next to it to avoid indentation on the plate. When the molding die is not in use, please take out the oil from the machine tool and store the mold cabinet Inside, prevent rust and dust from causing mold damage.
- The full molding of the mold requires micro-distance adjustment, and the operator must be patient and careful in this process. The fine-tuning methods are:
- The stroke of the CNC punch press cannot be adjusted, and only the height of the die striking head assembly can be adjusted;
- The stroke of the CNC punch press can be adjusted, and the requirements can be met only by modifying the machine parameters during programming;
- Please adjust the height of the mold striking head assembly when adjusting the large distance.
- For high forming or unconventional forming molds, please do a good job of lubricating both sides of the sheet to enhance the fluidity of the sheet during forming and reduce the chance of sheet rupture.
- When programming, be sure to use the molding die processing program, reserve enough unloading time when programming, and set the punching speed to the slowest, low-speed impact, so that the formed material has enough time to separate from the mold to avoid the plate Deformation and forming position deviation.
- The forming position of the plate should be as far away as possible from the clamps and punching parts, and the forming of the plate should be completed after the stamping process as far as possible.
- Using other forming dies around high forming dies, or continuing processing with standard punching dies will result in sheet deformation.
- The high forming mold has the phenomenon of scratches and collisions on the plate, resulting in deformation. Placing balls on both sides of the high forming mold lower mold auxiliary transition can avoid this problem.
Reasons and solutions for large burrs of CNC punching machines
In the process of sheet metal processing, the big problem of CNC punch blanking burr seriously affects the quality and production efficiency of sheet metal parts.
Causes of glitches:
blunt edge
- The material and surface treatment of the convex and concave molds are not good, and the wear resistance is poor;
- The die structure is poor, the rigidity is poor, causing gnawing;
- If it is not lubricated in time during operation, it will wear quickly;
- The cutting edge is not sharpened in time.
Blanking gap
- Mold manufacturing errors, die parts processing does not conform to the drawings, and the parallelism of the bottom plate is not good;
- The mold assembly error, the large gap of the guide part, the non-concentricity of the convex and concave mold assembly, etc.;
- The accuracy of the press is poor, such as the gap between the guide rails of the press is too large, the parallelism between the bottom surface of the slider and the surface of the worktable is not good, or the verticality of the slider stroke and the tabletop of the press is not good, the rigidity of the worktable is poor, and the Deflection occurs during cutting, which can cause changes in the gap;
- Installation errors, such as the surface of the upper and lower bottom plates of the die is not wiped clean during installation or the fastening method of the upper die of the large die is improper, and the upper and lower dies of the die are not installed concentrically (especially the die without guide column), which causes the working part to tilt;
- The structure of the die is unreasonable, the rigidity of the die and the working part is not enough, the punching force is unbalanced, etc.;
- The curvature of the steel plate is large and the steel plate is uneven.
The material does not meet the technical requirements
The material thickness is seriously out of tolerance or the wrong material (such as the wrong steel grade) is used to cause the relative clearance to be unreasonable and cause burrs to occur in the workpiece.
The large burr of sheet metal parts is usually produced in the process of sheet metal blanking. By improving the stamping conditions and sharpening the die, the four sides are sharpened, which can avoid the generation of burrs.