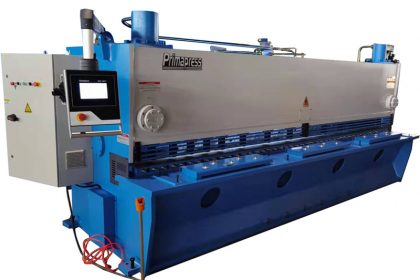
Components Repair method and maintenance of sheet metal hydraulic plate shearing machine
The components and functions of the hydraulic plate shearing machine actuator
The conveying mechanism of the hydraulic plate shearing machine mainly converts the torque output by the engine into the power of the roller to convey the sheet material. The transmission of the pulley is mainly used here. Because the transmission ratio is easy to control, and the conveying sheet material is light, so The required transmission torque is not very large, and the solution is to use pulley transmission. Because an intermittent mechanism is required, a pair of incomplete gear transmissions are added to the transmission to realize the intermittent transmission of the mechanism.
The two main parts of the actuator are the planetary gear and the six-bar mechanism. The six-bar mechanism must be tested first to determine the length of each rod, and at the same time meet the rod length requirements of the crank-rocker mechanism, and then calculate the transmission angle. The length of each rod is adjusted by the size of the transmission angle. In this way, the length of each rod of the six-bar mechanism is determined. Brief description of the connection between the conveying mechanism and the actuator: To make the conveying mechanism and the actuator just meet the requirements, it is necessary to make the incomplete gear in the center of the locking arc during installation, and the cutter just finishes cutting the sheet.
Safety precautions during the use of the hydraulic plate shearing machine:
(1) Before working, carefully check whether the various parts of the shear trigger are normal, whether the electrical equipment is in good condition, whether the safety protection device is reliable, and whether the lubrication system is smooth, and then add lubricating oil, test the car, and the car can be used in good condition. When two or more people are working together, it is necessary to make sure that one person is in command, and the machine tool can only be started when there is no obstacle in the table and its surroundings. The hydraulic plate shearing machine is not allowed to cut two sheets of different specifications and materials at the same time. It is forbidden to cut without material. The surface of the board to be cut should be flat, and it is not allowed to cut the narrower board that cannot be compressed.
(2) Concentrate when operating the hydraulic plate shearing machine. When feeding, the fingers should be 200mm away from the knife edge and the pressing device. Feeding and reclaiming materials should prevent the steel plate from being scratched, and prevent the steel plate from being cut off and hurting people. The foot switch should be equipped with a sturdy protective cover to prevent heavy objects from falling on the foot switch or stepping on it by mistake.
(3) All kinds of shears should be properly adjusted according to the specified thickness of the shearing plate to prevent accidents caused by improper use.
(4) The brake of the hydraulic plate shearing machine should be checked frequently to ensure reliability and prevent the upper knife edge from falling suddenly and hurting people due to the loosening of the brake.
(5) The edges of the sheet and the sheared strip are sharp, and sometimes there are burrs, which should be prevented from scratching.
(6) During the operation, safe hand tools are used to complete the operations of feeding, positioning, picking up and cleaning leftovers, which can prevent fingers from being crushed by the mold.
After the sheet metal hydraulic plate shearing machine is cut, it should be able to ensure the straightness and parallelism of the shearing surface of the sheared sheet, and minimize the distortion of the sheet to obtain high-quality workpieces. Its upper blade is fixed on the knife holder, and the lower blade is fixed on the worktable. A material support ball is installed on the worktable, so that the sheet will not be scratched when sliding on it. The back gauge is used for sheet positioning, and the position is adjusted by the motor. The pressing cylinder is used to press the sheet to prevent the sheet from moving during shearing. Guardrails are safety devices to prevent workplace accidents. The return journey generally relies on nitrogen, which is fast and has a small impact.
Troubleshooting of sheet metal shears:
- Ask the equipment operator to understand the operation status of the hydraulic system equipment of the sheet metal hydraulic plate shearing machine. These include: whether its hydraulic system works normally; whether the hydraulic pump is abnormal; the time and result of the hydraulic oil detection cleanliness; the cleaning and replacement of the filter element; whether the hydraulic components have been adjusted before the failure; ; What abnormal phenomena have occurred in the hydraulic system of the machine before and after the failure; what failures have occurred in the system in the past, and how to eliminate them, etc., need to be understood one by one.
- Look at the actual working conditions of its hydraulic system, and observe whether there are any problems with system pressure, speed, oil, leakage, vibration, etc.
- Listen to the sound of its hydraulic system, such as: impact sound; pump noise and abnormal sound; judge whether the hydraulic system is working normally.
- Touch the temperature rise, vibration, crawling and the tightness of the joint to determine whether the working state of the moving parts of the hydraulic system of the sheet metal hydraulic plate shearing machineis normal.
Maintenance of sheet metal shears:
- Operate in strict accordance with the operating procedures;
- Add lubricating oil regularly, fixed-point and quantitatively according to the requirements of the lubrication chart before each startup, and the oil should be clean and free of precipitation;
- The machine tool must always be kept clean, and the unpainted part of the anti-rust grease;
- The lubricating oil in the motor bearing should be replaced and refilled regularly, and the electrical parts should be checked regularly to see if the work is normal, safe and reliable;
- Regularly check whether the V-belts, handles, knobs and buttons are damaged. If they are seriously worn, they should be replaced in time and reported for spare parts.
- Regularly check and repair switches, insurances, handles, and ensure their reliable work;
- 10 minutes before leaving get off work every day, lubricate the machine tool and scrub and clean the machine tool;
- It is strictly forbidden for non-designated personnel to operate the equipment. Usually, people must leave the machine and stop.