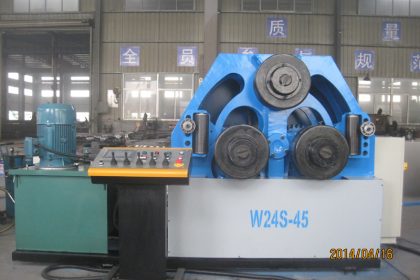
Characteristics and safe operation rules of CNC hydraulic metal profile bending machine
The profile bending machine has the following characteristics (Primapress profile bending machine):
- The equipment is equipped with 3 driving rollers, all of which are driving wheels. This prevents the profile from slipping in the rollers. To
- It can easily bend various profiles such as angle steel, channel steel, round pipe, square pipe and so on. …
- All products can be bent and formed at one time, with high efficiency and no wear; they can also be bent and formed as many times as needed;
- The three sets of rollers are all controlled by CNC numerical control devices, which move smoothly and can be accurately positioned. Positioning accuracy: +/-0.02mm. To
- The fixed driving wheel spacing can be adjusted in different positions according to user needs, that is, the positions of the two rollers can be adjusted to different spacings. To
- It can bend one radius arc (ordinary C-shaped arc), two radius arcs (U-shaped arc), and three radius arcs (bread arc and ellipse).
- It has the function of intelligent calculation and compensation of material rebound amount. For different radius bends, the equipment can automatically calculate the amount of springback. In this way, it is unnecessary to waste too much material and time when bending different arcs. To
- The device can store a certain amount of programs (depending on the memory space), and enter as detailed information as possible in the program for convenient and easy identification the next time it is used. To
- The equipment adopts horizontally placed profiles that can adapt to different sizes and weights. To
- It can be controlled manually or automatically, and the operation is flexible.
Primapress specializes in the production of profile bending machines, also known as roll bending machines and profile bending machines. The arc down-adjustable three-roll profile bending machine produced by our company is a kind of general equipment dedicated to the bending and forming of various profiles. It can roll the profile into round, arc, spiral and other workpieces. It is widely used in various industries such as chemical industry, hydropower, shipbuilding machinery manufacturing and large-scale steel structure construction. However, when the operator uses the profile bending machine, he should use it in accordance with the safe operating procedures:
- The operator should understand the structure and performance of the profile bending machine, and be proficient in the operation method of the control system and the bending process of the workpiece, and strictly abide by the safety operation items.
- Before starting the profile bending machine, please carefully check whether the motor, switch, circuit and grounding are normal and firm. Check the control parts of the equipment and whether the button position is correct. Check whether the mold meets the processing requirements.
- During operation, if irregular noise, impact, swing or oil leakage is found, stop immediately for inspection and repair.
- Operators must tie their clothes and cuffs tightly, and it is strictly forbidden to tie aprons or noodles to work; long-haired women should tie their hair and wear a hat when working to prevent safety accidents from being twisted in.
- When operating the equipment, the operator’s hands and other parts of the body should not be more than 20cm closer to the roller, and it is strictly forbidden for non-operators to stay in front of the equipment.
- The equipment must be used within the capacity of the equipment, and overloading is not allowed.
- The profile bending machine adjusts the position of the roller according to the diameter of the roll circle, and debugs with waste materials before the operation, and does not directly take the workpiece for debugging.
- When the profile is bent, it must be compacted to prevent the profile from warping and being injured when it is bent.
- If the machine or mold is found to be incorrect during operation, the calibration should be stopped. It is strictly forbidden to make corrections by hand during operation to prevent injuries.
- After the operation is completed, the power supply should be cut off and the power supply box should be locked.
- The hydraulic transmission system should be checked regularly, and the failed hydraulic components should be adjusted and replaced in time.
- The fuel tank should maintain the specified oil level, minimize the pollution of the hydraulic oil, check the deterioration of the hydraulic oil at least half a year, and replace it in time if it exceeds the regulations.
- All live parts of the electrical system should be properly grounded, electrical components should be inspected regularly, dust removed, and damaged and invalid components should be replaced in time. All solenoid valves and stoppers should be checked and adjusted frequently.