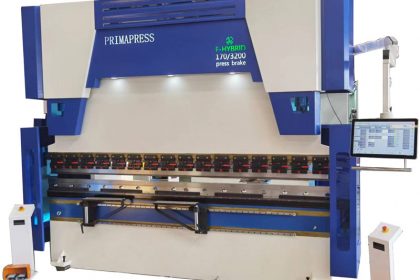
Advantages and characteristics of hybrid cnc press brake bending machine
The oil-electric hybrid cnc press brake bending machine includes a power unit and a control valve group connected with the CNC system. The power unit includes a servo motor, a one-way quantitative pump connected with the servo motor, and an independent fuel tank; the control valve group includes a relief valve, a discharge valve Load valve, check valve, reversing valve, back pressure valve, poppet valve, safety valve and filling valve. The speed of the servo motor of the power unit is controlled by the numerical control system, and then the displacement of the oil pump connected to it is controlled, so as to realize the displacement speed control of the actuator (double-rod oil cylinder). Through the numerical control system to set the torque of the servo motor, the control of the output force of the left and right actuators (double-rod oil cylinder) is realized.
Hybrid cnc press brake bending machine
The displacement readings of the left and right actuators (double-rod oil cylinder) are fed back to the numerical control system through the displacement sensor (grating ruler or magnetic grating ruler). Closed-loop control of synchronization and positioning of oil cylinders). The displacement sensor constitutes an internal feedback link to improve the control accuracy of the system.
Advantages of oil-electric hybrid electro-hydraulic system
Since the motor does not rotate when the hybrid cnc press brake bending machine is in standby, the machine is in a state of zero noise when it is not working; because the oil consumption of the hybrid CNC machine is only one-third of that of the electro-hydraulic synchronous machine, and the oil temperature Controllable, so it is generally not necessary to replace the hydraulic oil within three years; because the frequency response of the servo motor is much higher than that of the proportional valve, the time of one bending cycle of the hydraulic-electric hybrid cnc press brake bending machine is 30 faster than that of the electro-hydraulic synchronous cnc press brake bending machine. %.
Through the comparison of the two control methods, we can clearly see that the oil-electric hybrid numerical control (pump control) system has the characteristics of high efficiency and energy saving, high precision, low noise, and environmental protection. The specific advantages include the following 10 points.
⑴Pump control technology replaces conventional valve control technology, eliminates throttling loss, has no overflow loss, and saves energy significantly;
(2) The servo motor can be significantly overloaded in a short time, and the actual installed power is only 50% of the theoretical installed power;
⑶ The volume of the fuel tank is reduced by 75%, which greatly reduces the use of hydraulic oil;
⑷The thermal equilibrium temperature is low, no cooling device is required, and the life of hydraulic components is prolonged;
⑸The noise is obviously reduced in idle, fast down, pressure holding, and return state, and the working environment is improved;
⑹The response speed of the servo motor is faster than that of the ordinary motor, and the pressure and flow switching are faster in emergency;
⑺The sensitivity of oil particles is reduced, from NS7 grade to NS9 grade;
⑻Temperature sensitivity decreases, the working temperature is widened from -10 to 60°C to -10 to 80°C;
⑼ Under certain conditions, the maximum speed of fast down and return can reach 300mm/s;
⑽The working speed can be greatly increased, up to 20-25mm/s.
The oil-electric hybrid cnc press brake bending machine has better synchronization, real energy saving and high efficiency, simple structure and faster speed, but the price is high, how to achieve reasonable cost and stable performance, that is, the higher cost performance is the formation of batches by enterprises production and the premise of market acceptance.
What are the advantages of the electro-hydraulic servo pump-controlled cnc press brake bending machine system?
The pump-controlled servo cnc press brake bending machine includes a power source and a control valve group connected with the numerical control system. It is characterized in that the power source includes a servo motor, a two-way quantitative pump connected with the servo motor, and an oil tank; the control valve group includes a shuttle valve and adjusts the system pressure. pressure valve, unloading valve, check valve, reversing valve, back pressure valve, poppet valve, safety valve and filling valve; the oil inlet and outlet of the two-way quantitative pump are controlled by the shuttle valve, and the positive oil outlet It is directly connected to the upper chamber of the oil cylinder, and the reverse oil outlet is connected to the lower chamber of the oil cylinder through the poppet valve and the back pressure valve; the oil inlet and outlet of the bidirectional quantitative pump are connected to the oil tank through the check valve, reversing valve and filling valve; the filling valve is connected Control valve; a safety valve is connected between the oil tank and the lower chamber of the oil cylinder. It has the characteristics of high efficiency and energy saving and high synchronization accuracy.
cnc press brake bending machine
PRIMAPRESS feels the advantages of electro-hydraulic servo pump control hybrid system:
- Pump control technology replaces conventional valve control technology, eliminates throttling loss, has no overflow loss, and saves energy significantly;
- The servo motor can be significantly overloaded in a short time, and the actual installation power is only 50% of the theoretical installation power
- The volume of the fuel tank is reduced by 75%, reducing the use of hydraulic oil
- The thermal equilibrium temperature is low, no cooling device is required, and the life of hydraulic components is prolonged
- The noise is obviously reduced in idle, fast down, pressure holding, and return state, and the working environment is improved
- The braking speed of the servo motor is faster than that of the ordinary motor, and the pressure and flow are cut off quickly in an emergency.
- The oil particle sensitivity is reduced from NS7 to NS9
- The temperature sensitivity decreases, and the working temperature is extended from -10°C–60°C to -10°C–80°C
- The speed matching is very high, the same valve group, with 6, 8, 10 three kinds of pumps can cover 30-300 tons of bending machines
- Under certain conditions, the maximum speed of fast down and return can reach 200mm/s
- The working speed can reach 200mm/s