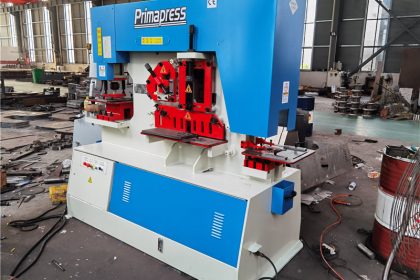
Safety operation of hydraulic ironworker combined punching and shearing machine
content validity
hydraulic ironworker combined punching and shearing machine and mechanical profile punching and shearing machine combine the functions of punching, shearing plate angle steel, profile shearing, etc. They have the advantages of light weight, small volume, low noise, etc. They are ideal equipment for modern machinery manufacturing industries such as metallurgy, bridge, communication, power, etc.
Pre preparation before startup
1) Each transmission part shall be lubricated sufficiently, and each lubrication point shall be refueled 2-3 times per shift
2) The cutting tool and punching die shall be intact, free from cracking, and firmly fastened;
3) The clearance between the punch and the die hole wall shall be uniform and meet the punching and shearing requirements. The minimum configuration of the punch shall be slightly higher than the die hole plane;
4) The electrical insulation and grounding of the equipment are good.
Operating procedures and specifications
Operating Steps
1 Check the power supply, the voltage is stable, there is no phase loss, and the leakage protector and air switch are in good condition.
2 Wiring: open the connection cabinet of the hydraulic ironworker combined punching and shearing machine, connect the wires and close the cabinet door.
3 After power on, step down the foot switch, the machine does not move, exchange the power lines, and check whether the emergency stop switch is turned on.
4 Connect foot pedal switch.
5 During operation, please turn off the power every time you change the mold
6 After the work is completed, turn off the switch, turn off the main power switch, skim the power line and clean the debris.
Safe operation specification
1 Punching and shearing of steel plate, round steel, square steel and section steel shall be conducted at the same time. However, it is not allowed to cut two kinds of steel at the same time.
2 It is strictly prohibited to cut hardened steel and process beyond the capacity of the equipment.
3 The cutting tool and cutting edge should be kept sharp, and should be replaced in time if the cutting edge becomes blunt or cracks.
4 Shear steel plate, round steel and square steel. The section steel must be pressed tightly.
5 When shearing or punching, it is strictly forbidden to touch the surface of the rotating parts, measure the workpieces, and directly clean the leftovers.
6 The operator must stop the machine when leaving the machine tool, and check that the original position of the handles of each part is unchanged when starting again.
7 It is not allowed to cut the laminated sheet, trim the edge of the rough edge sheet, and cut the narrow sheet and short sheet that cannot be pressed tightly.
8 When two or more persons work together, one person must command uniformly and act in the same way.
9 When using materials, the fingers must be 200mm away from the knife edge, and small pieces should use special tools;
10 The operator shall concentrate, and it is forbidden to connect the vehicle.
11 It is not allowed to load materials from the opposite side of the control lever.
Handling of abnormalities and emergencies
1) It is strictly forbidden for non designated personnel to operate the equipment, and people must leave the machine and stop.
2) Turn off the power and clean the work site.
3) Check the equipment to ensure that it is in good condition and carry out daily maintenance as required.
Maintenance rules
- Operate in strict accordance with the operating procedures.
- Before each startup, add lubricating oil regularly, fixedly and quantitatively according to the requirements of the lubrication chart. The oil should be clean and free of sediment.
- The plate shears must always be kept clean, and the unpainted parts of the anti rust grease must be kept clean.
- The lubricating oil in the motor bearing shall be replaced and filled regularly, and the electrical equipment shall be checked regularly for normal, safe and reliable operation.
- The shop keeper shall check whether the triangle belt, handle, knob and key of the shearing machine are damaged. If they are seriously worn, they shall be replaced in a timely manner and the spare parts shall be reported for supplement.
- Regularly check and repair switches, fuses and handles to ensure their reliable operation.
- The machine tool shall be oiled, lubricated and cleaned 10 minutes before going off duty every day.