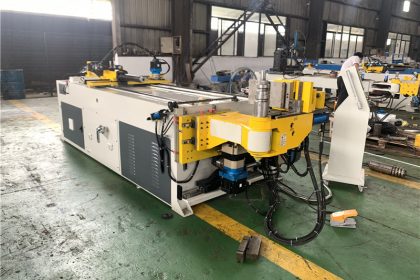
Common problems and solutions of automatic CNC pipe tube bending machine
Machine tool equipment enterprise pipe bender product introduction
Our pipe bender machine tool equipment undergoes multiple processing procedures and undergoes final assembly. Before the final assembly of the equipment, the cabinet of the equipment must be polished and painted, and then the parts are processed. A series of processing such as blackening, chrome plating, heat treatment, etc. Finally, the parts are assembled by drilling and tapping teeth.
Each step here must be completed in strict accordance with the technical requirements of the machinery and equipment, without any loopholes and errors. After the installation of the machine is completed, we start the connection of the wiring. This part is separated. The electrical part must be an electrician. The pipe bender machine assembly technician is responsible for the hardware installation of the pipe bender. After the hardware is installed. Then the electrical wiring of the rear machine is connected to the hydraulic system pipeline and so on.
The reason for separating the two parts is to obtain a more detailed installation process and equipment safety standards for the pipe bender. The group is all responsible for the end, so that unskilled knowledge will lead to failure in a certain area, thereby reducing the safety and stability of the pipe bender.
After these years of training, our company has a large scale and strong technical force. It is fully capable of independent production, R&D and sales as an integrated modern enterprise. Wait, the field of pipe processing machinery has reached a very standard level. In the research and development of equipment, we have already started the research and development of numerical control automation and completely independent production.
Let’s talk about the possible failures and troubleshooting methods of the fully automatic CNC pipe bending machine:
- Malfunction: After the piston rod stretches out a certain length, shake the handle, and the top rod stretches and shrinks. Cause: The fuel filler plug is not loosened, loosen the fuel filler plug. Elimination method: The oil outlet valve port in the pump body is not sealed and the oil outlet valve steel ball is not round. There is garbage in the oil. Change the clean oil and replace the steel ball.
- Malfunction: oil seepage at the piston rods of the large and small pumps. Cause: the sealing ring is damaged; troubleshooting method: replace the sealing ring in the spare parts bag.
- Fault: oil seepage at the switch; cause: the pressure ring inside the switch is too loose; troubleshooting method: after removing the limit screw and switch, tighten the pressure ring.
- Malfunction: The ejector rod is weak and cannot work. Cause: The steel ball in the switch is not well sealed. The top of the switch does not hold the steel ball or the steel ball is dropped; troubleshooting method: replace the steel ball and tighten the switch. If there is no steel ball, add a steel ball.
- Fault: oil leakage at the top of the ejector rod; cause: the sealing ring at the top of the piston rod is damaged; troubleshooting: replace the 14×2.4 O-ring seal (provided by yourself)
- Malfunction: Insufficient oil suction of large and small pumps; Cause: Garbage or insufficient oil is attached to the filter screen in the filter; troubleshooting: unscrew the 12 serial number parts, clean the mesh body with gasoline and fill up the oil.
- Malfunction: The mold mounting hole is cracked; the cause: there is a side load when the mold item is out, such as: the position of the bent workpiece is not set when it is bent again; troubleshooting: check whether the positions of the two supporting wheels are symmetrical, the supporting wheel and Apply oil to the joint of the workpiece, and put it in the correct position for the second bend.
- Malfunction: Picking up the pump is also called pumping and returning the pump; cause: the steel ball of the delivery valve cannot be reset normally; troubleshooting: extend the acting rod (15) to make the plunger pump have pressure, place it on the handle seat (14) The valve ball can be reset by tapping a few times with the upper head.