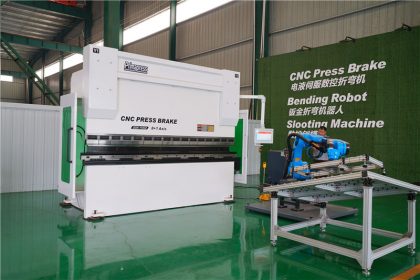
Why buy a sheet metal cnc press brake bending robot?
Metal sheet cnc press brake bending robots and automation are the investment choices of many companies to improve production quality, improve the working environment,
and make up for the shortage of workers. Many people think that the purchase of robots is mainly to replace workers, but in fact, we rarely see cases where the purchase of robots
leads to the lay-off of employees. The prejudice we get about robots from the media is that the main job of robots is to replace human workers. In fact, most companies are not like that.
The 8 most common reasons to invest in sheet metal cnc press brake bending machine robotics and automation
1. Increase productivity
After working with a sheet metal cnc press brake bending robot, the company is usually able to increase production at the same cost as before. However, this does not
mean that these labor are redundant. Robots are usually assigned to the most repetitive tasks, while employees have time to focus on those tasks that add more value to the product.
2. Speed up production
Many companies invest in robots to optimize task execution and speed up production time. This is especially important when customers expect shorter time from order to
delivery. Robots usually work uninterrupted, and in some cases even faster than employees, as long as tasks are simple, such as cnc press brake bending metal sheets or packaging
and palletizing final products.
Once the speed of each process increases, the rest of the production must keep up. Only when the automation process eliminates the bottleneck or increases the speed of all
processes before and after the robot, the total production time will decrease. Many companies still ignore this when investing in robotics and automation solutions.
If the completed unit must wait a few minutes before being received by the next process, it doesn’t make much sense to save a few seconds by automating the process.
3. Improve cnc press brake bending quality
In many cases, robots can produce a more consistent result than different employee shifts. Robots are programmed to repeat exactly the same actions, so many companies
use robots to improve product quality.
This does not mean that robots are more like craftsmen than humans. Usually, it is difficult for them to complete complex tasks, which require particularly good craftsmanship.
But in those situations where you have to repeat a simple task multiple times, industrial robots may provide a more uniform and consistent result.
4. Improve working conditions
The assembly line production is an amazing invention, which makes the production method more efficient than before. However, all these efficiencies have a caveat:
workers are faced with a lot of repetitive work, and often tired work. Some companies try to solve this problem, requiring employees to rotate at certain intervals between
different tasks so that they don’t have to repeat the same heavy actions too many times.
For many people, robotics and automation are the next step, a solution to reduce the burden on employees and improve working conditions. For example, in a dangerous
work environment, robots are a wise choice. But usually, this is just to take over the tedious work and let people do more meaningful work.
5. Gain robot experience
Once you try new things, it is always encouraging to start with a success story. The same goes for your first investment in robotic cnc press brake bending automation.
We see that more and more companies choose to start with low-risk projects when buying their first robot.
In these situations, robots may not be able to immediately improve production efficiency. The purpose is to become familiar with this technology and to cultivate
people’s skills in handling this technology. Once the company has invested a lot of money in robots, this experience will come in handy. If the senior management has a
strategic goal of automated production, then it is very reasonable to start from a low starting point and build from there.
6. Preemptive strike
To be honest: Most companies buy robots to improve production efficiency. For them, robotics is a question about using off-the-shelf technology to automate
well-documented processes.
However, in rare cases, companies will also strategically use robots to gain first-mover advantage. These companies choose to invest in high-risk development projects
because they are making a deliberate bet, hoping to become the first company in the market to benefit from new automation solutions.
However, becoming a pioneer is risky. This is why few people can afford it, and only those companies that can tolerate project failures and higher than
expected costs can afford it. On the other hand, in some industries, such as the agricultural and pharmaceutical industries, it is necessary to become a pioneer.
If the industry is strictly regulated, it may take years for new solutions to be approved. If you limit yourself to existing technologies, you may be obsolete by the time
you get approval. A development project may be more likely to be the most recent after approval.
Finally, advanced robotic solutions also have some decorative purposes that cannot be ignored. Production sites full of robots are easier to win the trust of
customers-they are a sign of well-functioning and efficient production.
7. Make up for the shortage of workers
Not all companies can keep up with demand. The shortage of workers can be a real obstacle to the development of the company. This is why robotics and automation
solutions are sought after by those who have difficulty finding qualified workers.
When it comes to specific areas such as welding, advanced assembly or quality control, finding people with the appropriate skills and experience can be very challenging.
The company can then double its production capacity by using welding robots carefully guided by skilled welders. The welder teaches the robot what to do, and its advantage is
that it can accurately execute instructions. In this way, the company can use its in-house expertise to improve its production capacity.
8. Avoid outsourcing
If you cannot break even, outsourcing production lines to low-income countries is usually the end result. But there is another way: by optimizing production processes
and investing in robotic cnc press brake bending equipment, some companies may delay or even avoid outsourcing to other countries.
This has several advantages, one is that the production is closer, and it can respond quickly to unforeseen events. Automated production can reduce some costs related to
outsourcing, such as freight, travel expenses, delayed shipments, and so on. In addition, by avoiding outsourcing, companies in outsourcing destinations are less susceptible
to rising wages, worker shortages, and other unforeseen factors.